فرایند ساخت اسکلت فلزی در کارخانه
مزایای استفاده از اسکلت فلزی نسبت به بتنی چیست؟ مراحل ساخت اسکلت فلزی در کارخانه چگونه است؟
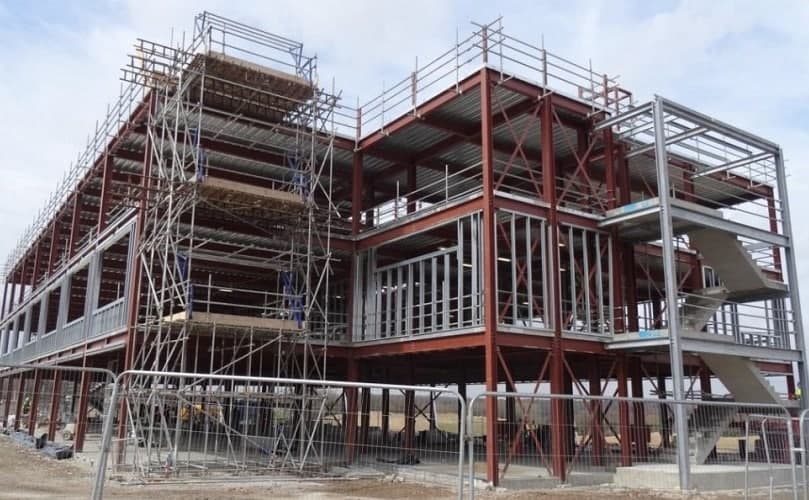
عملیات ساخت و اجرا با سریعتر و راحتتر از اسکلت بتنی انجام میشود. کیفیت بیشتر، سرعت ساخت بالا، کاهش پرت مصالح و مقاومت بالای آن از جمله مزایای استفاده از اسکلت فولادی است. اسکلت فولادی ساخته شده در کارخانه به علت رعایت تمامی ضوابط و و استفاده از تجهیزات، ایمنتر و باکیفیتتر است.
ما در این مقاله به بررسی نحوه ساخت اسکلت فلزی در کارخانه، نمونه نقشه شاپ اسکلت فلزی به همراه فایل های صوتی و 6 ویدئو جامع می پردازیم.
⌛ آخرین بهروزرسانی: 29 دی 1400
? تغییرات به روز رسانی: انتشار جدید
در این مقاله چه میآموزیم؟
شکل 1-اسکلت فولادی
لطفاً قبل از خواندن این مقاله به توضیحات فایل صوتی زیر گوش دهید
-
مزایای استفاده از اسکلت فولادی
در حال حاضر ساختمانها در کشور به دو روش اسکلت فلزی و اسکلت بتنی ساخته میشوند که انتخاب هرکدام از این دو روش به فاکتورهای متعددی نظیر منطقه آبوهوایی، میزان بودجه، شرایط و کیفیت اجرا، مسائل فنی سازه و … مرتبط است و تشخیص آن بر عهده مهندسین باتجربه است. مهندسین و کارفرمایان با بررسی عوامل مختلف، نوع اسکلتبندی بنا را تعیین میکنند. اسکلت فلزی از گذشتههای دور تا امروز در ساختمانها اجرا میشود و مزایای آن در برابر عوامل مختلف باعث شده این نوع اسکلتبندی در اکثر سازهها و ساختمانها به چشم بخورد. در ادامه به معرفی برخی از این مزایا میپردازیم:
1.1. سرعت اجرای اسکلت
همزمان با تخریب ساختمان قدیمی و اجرای گودبرداری، امکان ساخت اسکلت فلزی در کارخانه فراهم است؛ لذا سرعت اتمام پروژه بیشتر خواهد بود و طبیعتاً هزینههای زمانی پروژه کمتر و بازدهی مالی بیشتر خواهد بود.
2.1. سادگی نصب در محل
عملیات اصلی ساخت در کارخانه انجام میشود؛ لذا اسکلت فلزی در شرایط بسیار سادهتری نسبت به اسکلت بتنی در محل اجرا میشود. همچنین امکان کنترل کیفیت با استاندارد بالاتری در کارخانه فراهم میگردد.
3.1. بازدهی نهایی بیشتر
مدت عملیات اجرایی اسکلت فولادی نسبت به اسکلت بتنی کمتر است. در نتیجه باعث اتمام سریعتر پروژه و طبیعتاً کاهش هزینههای سربار و رسیدن به سود نهایی سریعتر و بیشتر، میگردد. همچنین به دلیل اینکه در اسکلت بتنی، ابعاد ستونها تقریباً ۳ برابر بزرگتر از ستونهای اسکلت فولادی است، لذا زیربنای مفید بیشتری به ساختمان اضافه میگردد. این امر باعث بهبود کیفیت فضاهای معماری و داخلی برای مصرفکننده نهایی میگردد.
-
انواع اسکلت فلزی
انواع اسکلت فلزی به نوع اسکلت فلزی پیچومهرهای و اسکلت فلزی جوشی تقسیم میشود.
1.2. اسکلت فلزی پیچ و مهرهای
در این نوع اسکلت فلزی، تمام ستونها و تیرهای فولادی از قبل در کارخانه و یا کارگاه تولید شده و بعد به محل ساخت و ساز فرستاده میشوند. در آنجا ستونها و تیرهای فولادی بهوسیله پیچ و مهره به هم متصل میشوند و در نهایت، اسکلت فلزی اولیه ساختمان را شکل میدهند. اسکلت فلزی پیچومهرهای بهترین اسکلت فلزی در بین بقیه اسکلتها است. سرعت ساختمانسازی با اسکلت فلزی پیچومهرهای بهمراتب بیشتر از بقیه انواع اسکلت فلزی است. زیرا تنها کاری که نیاز است در محل ساختوساز انجام شود آوردن تیر و ستونهای فولادی و پیچ و مهره کردن آنهاست.
از دیگر مزایای استفاده از پیچ در سازههای فلزی پیچ و مهرهای میتوان به عدم ایجاد تنشهای پسماند مشابه اتصالات جوشی، امکان باز نمودن سازه و استفاده مجدد، عدم نیاز به کارگر ماهر، محدودیت در تأمین وسایل و و بیسروصدا بودن هنگام نصب و اجرا اشاره کرد؛ اما مشکل عمده در اجرای سازههای فولادی با اتصالات پیچی، اجرای نامناسب سوراخها و عدم رعایت میزان نیروی پیش تنیدگی میباشد. در ادامه با اتصلات اتکایی و اصطکاکی آشنا خواهید شد.
شکل 2- اسکلت فلزی پیچ و مهرهای
1.1.2. اتصال اتکایی
در عملکرد اتکایی، پیچ درون سوراخ صفحات اتصال قرار میگیرد و مهره بسته میشود. هنگامی که بار خارجی به پیچ وارد میشود، قطعات اتصال، لغزش پیدا میکنند که در اثر آن، یک نیروی فشاری به لبههای اتصال وارد میشود که تبدیل به نیروی برشی در پیچ میشود. این اتصال، تنها برای حالت بارگذاری ثقلی است و در طرح لرزهای نباید از این نوع عملکرد در اتصال استفاده نمود. در این نوع اتصال، هیچ نیروی پیش تنیدگی در پیچ ایجاد نمیشود و برای اجرای این اتصال، تنها سفت کردن پیچ بهوسیله کارگر کفایت میکند.
سوله ایران یکی از بهترین کارخانه اسکلت فولادی و سوله سازی در کشور است که مجهز به دستگاه های مختلف تولیدی است و از پرسنل تخصصی و باتجربه برای تولید سازه های فلزی استفاده می کند.
2.1.2. اتصال اصطکاکی
هنگامی که پیچ درون سوراخ صفحات اتصال قرار میگیرد، علاوه بر مهره باید از واشر نیز استفاده نمود. باید توجه شود که واشر مصرفی در اتصال اصطکاکی نباید از نوع واشر فنری باشد. در طراحی لرزهای تنها باید از این فلسفه طراحی در اتصال استفاده شود. بهعبارتیدیگر، در طراحی همه اتصالات قابهای خمشی و قابهای دوگانه و نیز اتصالات بادبندی و وصله ستونهای باربر جانبی در قابهای ساده باید از این نوع عملکرد استفاده نمود.
در این نوع اتصال، علاوه بر سفت کردن اولیه پیچ، باید به مقداری که در طراحی مشخص شده، نیروی پیش تنیدگی نیز در پیچ ایجاد شود. با اعمال نیروی پیش تنیدگی، پیچ تحت کشش قرار گرفته و با اعمال بار، بین صفحات اتصال، اصطکاک به وجود میآید که باعث عدم لقی و کارکرد کامل اتصال میشود.
زمانی که یک پیچ پر مقاومت بدون کشش اولیه، تحت اثر نیروی کششی خارجی قرار میگیرد، نیروی کششی درون پیچ با نیروی اعمال شده برابر میشود. درصورتیکه پیچ پیشتنیده (پیش کشیده) شده باشد، درصد بسیار زیادی از نیروی کششی خارجی صرف ایجاد نیروهای فشاری و یا گیرهای اعمال شده به اجزای اتصال میشود.
به دلیل آن که به طور معمول، کشش به وجود آمده در پیچهای پرمقاومت ناشی از نیروی کششی خارجی در لحظه جداشدن قطعات از یکدیگر نزدیک به ده درصد بیش از کشش در آغاز بارگذاری است، لذا باید همه پیچهایی که تحت اثر کشش مستقیم قرار دارند، پیش کشیده شوند.
باتوجهبه میزان مقاومت نهایی کششی مصالح پیچ، پیچها به دو دسته زیر تقسیم میشوند:
- پیچهای معمولی
• پیچهای پر مقاومت
شکل 3 – دستهبندی پیچها بر اساس مبحث 10 مقررات ملَی ساختمان
شکل 4 – پیچ پرمقاومت 8.8
2.2. اسکلت فلزی جوشی
در انواع اسکلت فلزی جوشی همه مراحل کار در محل ساخت و ساز انجام میپذیرد. قطعات تیر و ستونها در محل ساختوساز برش خورده و برای ایجاد شکل نهایی اسکلت فلزی این تیر و ستونها به هم جوش زده میشوند. برای ایجاد انواع اسکلت فلزی جوشی بهتر است جوشکارهای متخصص به کار گرفته شوند.
شکل 5- اسکلت فولادی جوشی
3.2. مزایای اسکلت فلزی پیچ و مهرهای نسبت به جوشی
برخی از مزایای اجرای اسکلت فلزی با پیچ و مهره عبارتند از:
▪️ سرعت اجرای بالا:
سرعت اجرای اسکلت فلزی پیچومهرهای باتوجهبه حذف جوش و جایگذاری ساده قطعات در محل نصب و اتصال ساده پیچومهره که نیاز به مهارت خاصی ندارد، نسبت به سازه فلزی جوشی بالاتر میباشد.
▪️ افزایش کیفیت ساخت:
در اسکلت پیچومهرهای باتوجهبه اینکه ساخت قطعات در محل کارخانه تحت نظارت و بازرسی دقیق انجام میشود، نسبت به سازههای فلزی جوشی که در محل ساخته و نصب میشوند، کیفیت بالاتری را شامل میشود.
▪️ ایمنی و پایداری سازه:
اسکلت فلزی پیچ و مهرهای نسبت به دیگر اتصالات در سازه فلزی، مقاومت بهتری در مقابل زلزله از خود نشان میدهند.
▪️ هزینه کمتر:
باتوجهبه بازبودن دست طراح در کم کردن ضخامت و ابعاد قطعات و امکان استفاده از اتصالات خرپایی و پیچیده، میتوان انتظار داشت هزینه سازههای فلزی پیچومهرهای نسبت به جوشی پائینتر باشد.
▪️ عدم نیاز به فضای کار زیاد:
به علت انجام بخش بیشتر کار در کارخانه، قابلت اجرا در شلوغترین و کمحجمترین موقعیتها فراهم است.
▪️ رواج جهانی:
در امریکا و اروپا تقریباً تمام سازهها، پیچومهرهای هستند، مگر در شرایط خاص و کماهمیت بودن سازه که بهصورت جوشی اجرا میشود.
▪️ امکان استفاده در مدیریت حوادث:
باتوجهبه نصب و برپایی ساده آن، امکان جمع و جابهجایی آن در مواقع حوادث مانند سیل و آتشسوزی نیز میسر است.
-
انواع جوش و روشهای جوشکاری
جوشکاری در ساخت اسکلت فلزی چه در حین مراحل ساخت در کارخانه و چه در محل اجرا، یک بخش جداییناپذیر از آن است، برای ساخت و سرهم کردن قطعات به یکدیگر بهخصوص در سازههای جوشی، بسیاری از قطعات در داخل کارخانه جوش داده میشوند و معمولاً یک واحد جوشکاری در کارخانهها با تجهیزات کافی در نظر گرفته میشود. ازآنجاکه دقت جوش کارخانهای بسیار بالاتر است و در مواردی نوع جوش، جوشکاری و تجهیزات آن با جوشکاری در محل متفاوت است؛ آشنایی با انواع جوش، روشهای پراستفاده و متداول و کاربرد استفاده از هریک، امری ضروری میباشد.
جوشکاری اسکلت فلزی عبارت از اتصال و یکپارچه کردن مصالح با یکدیگر به کمک حرارت، با و یا بدون استفاده از فشار و یا مواد پرکننده اضافی است. به مصالحی که باید به هم متصل شوند، فلز مبنا و به مادهای که این اتصال را برقرار میسازد، فلز پرکننده یا فلز جوش گفته میشود. برای ذوب فلز مبنا و فلز جوش، حرارت به کار میرود تا مواد بهصورت سیال درآمده و تداخل آنها امکانپذیر شود. معمولترین روشهای جوشکاری، خصوصاً برای جوش فولاد ساختمانی، استفاده از انرژی برق بهعنوان منبع حرارتی است و بدین منظور اغلب از قوس الکتریکی استفاده میشود. قوس الکتریکی عبارت از تخلیه جریان نسبتاً بزرگ، بین فلز جوش (الکترود یا سیم جوش) و فلز مبنا است که از میان ستونی از مواد گازی یونیزه به نام پلاسما انجام میپذیرد.
در جوش قوس الکتریکی، عمل ذوب و اتصال با جریان مواد در طول قوس و بدون اعمال فشار صورت میگیرد. در ادامه به طور مختصر به معرفی انواع جوش پرداخته شده است اما برای مطالعه دقیق انواع روشهای جوشکاری شما عزیزان میتوانید به مقاله مراجعه کنید.
1.3. انواع جوش
- (Fillet weld)
• (Groove weld)
• جوش کام (Solt weld)
• جوش انگشتانه (Plug weld)
شکل 6 – انواع جوش
در زمینه ساختوساز، جوشهای گوشه و جوش شیاری به طور گستردهای در جوشکاری اسکت فلزی مورداستفاده قرار میگیرد. حدود ۸۰٪ از جوش گوشه و 15% از جوشهای شیاری استفاده میشود؛ 5% هم از جوشهای کام و انگشتانه استفاده میشود. جوشهای کام و انگشتانه برای انتقال برش در اتصالهای پوششی و یا جلوگیری از کمانش در عناصر رویهم آمده در اعضا ساخته شده استفاده میشود.
1.1.3. جوش گوشه در جوشکاری اسکلت فلزی
برخلاف جوش شیاری، جوش گوشه نیازی به آمادهسازی صفحات برای اتصال ندارد و هزینه اجرا را کمتر مینماید، جوش گوشه روی سطح صفحاتی که به هم دیگر متصل هستند به دو صورت پیوسته و منقطع انجام میشود؛ این جوش ممکن است فقط برای انتقال برش یا برای جلوگیری از انقباض یا جداسازی قطعات لبه استفاده شود.
شکل 7- جوش گوشه منقطع و پیوسته
2.1.3. جوش شیاری در جوشکاری اسکلت فلزی
جوش شیاری (Groove Weld)جوشی است که در شیار یا درز بین دو قطعه اجرا میشود. در این نوع جوش، میبایست لبه یک یا هر دو قطعه، قبل از جوشکاری از یک یا هر دو طرف آمادهسازی شود. جوشهای شیاری در داخل مقاطع عرضی ورقهایی که مجاور یکدیگر هستند، در اصطلاح، لببهلب و اتصال T استفاده میشود.
شکل 8 – جوش شیاری
اجرای جوش شیاری میتواند بهصورت یکطرفه یا دوطرفه باشد و بر اساس میزان نفوذ جوش در اتصال، به دو نوع نفوذ ناقص و کامل دستهبندی میشود.
- جوش شیاری لبه مربعی
• جوش شیاری نیم جناقی
• جوش شیاری جناقی
• جوش شیاری
• جوش شیاری لالهای
• جوش شیاری لبه اریب
از اشکال مختلف جوش شیاری میباشند. جهت تماس با گروه رویش کلیک کنید.
3.1.3. جوش کام و انگشتانه در جوشکاری اسکلت فلزی
از جوش کام برای پرکردن شکافها (مانند اجرای ورق های پیوستگی داخل ستون های جعبه ای) و از جوش انگشتانه برای پرکردن سوراخها (مانند اتصال ورق مضاعف به جان ستون) استفاده میشود.
شکل 9 – جوش کام(سمت راست) و جوش انگشتانه(سمت چپ)
شکل 11- از مدلسازی و شاپ(سمت چپ) تا واقعیت یک سازه فلزی (سمت راست)
شکل 14- نمونهای از کدها را در نقشههای شاپ
شکل 15 – نمونهای از جزئیات در نقشههای شاپ
جدول مشخصات پروژه:
در بخش پائین و سمت راست نقشههای شاپ نیز معمولاً مشخصات پروژه، پیمانکار، نام فرد یا شرکت طراحی و همچنین نام فرد یا شرکتی که شاپ پروژه را انجام داده، عنوان شده است.
شکل 16 – نمونهای از جدول مشخصات پروژه
شکل 17- نمونهای از جدول مشخصات پروژه
همچنین، نسخهای از نقشههای شاپ، در اختیار مونتاژکاران قرار میگیرد که حاوی اطلاعات موردنیاز برای اتصال تسمهها و پلیتها برای ساخت قطعات پروژه (تیرها، ستونها، دستکها و …) است.
در پروژههای اسکلت فلزی پیچومهرهای، قطعات و پلیتها باید سوراخکاری شوند تا هنگام نصب بتوان آنها را توسط پیچومهره به یکدیگر متصل نمود. عمدهترین فرایند سوراخکاری در یک پروژه، به سوراخکاری تیرها، بیس پلیتها (کف ستونها) و اسلایسها (پلیتهای اتصال) اختصاص دارد. برای سوراخکاری این قطعات، لازم است محل سوراخ و قطر آن را بدانیم. به همین منظور، جزئیات مربوط به این کار در نقشههای شاپ قطعات درج شده است و سوراخ کاران موظف هستند ابتدا بر اساس این نقشهها، مرکز سوراخها را علامتگذاری کرده و سپس با متههایی که قطر آنها مطابق با قطر سوراخ درج شده در نقشههای شاپ است، اقدام به سوراخکاری قطعات نمایند. در تصاویر زیر، برخی از نقشههای شاپ را مشاهده میکنید:
شکل 18- نمونهای از شاپ یک تیر
شکل 19- نمونهای از شاپ یک ستون
شکل 20- نمونهای از شاپ یک دستک
شکل 26 – نمونهای از نقشه شاپ سوله
شکل 28 – کارخانه ساخت اسکلت فلزی
2.5. مراحل تولید و ساخت اسکلت فلزی در کارخانه
1.2.5. برنامهریزی تولید
زمان یکی از ارکان مهم هر پروژهای میباشد و دستیابی به محصول باکیفیت در بازه زمانی مشخص اجرای پروژه مستلزم برنامهریزی زمانی دقیق میباشد. بدین منظور پس از تهیه نقشههای کارگاهی و مشخصشدن لیست قطعات، بر اساس اهمیت و نوع قطعه برنامه تولید قطعات در واحد برنامهریزی تدوین و بهصورت دستور کار، به خط تولید ابلاغ میگردد. در حین تولید نیز، اجرای برنامه مشخص شده مورد پایش قرار میگیرد.
2.2.5. قطعه زنی
شامل بازکردن رولها (در صورت نیاز)، تمیزکاری ورق، برشکاری، سوراخکاری و پخزنی است. ممکن است ورقهای خریداری شده، سطحی روغنی و زنگ آلود داشته باشند. برای ازبینبردن چربیها و زنگزدگی، بایستی سطح ورق تمیز شود. چراکه این آلودگیها کیفیت جوشکاری را پایین میآورد. در کارگاههای سنتی، قطعه زنی بر اساس یک جدول نهایتاً تهیه شده در اکسل صورت میگیرد. اما در یک کارخانه مدرن، قطعه زنی بر اساس نقشههای سینگل از تکلا استراکچر انجام میشود. مرحله قطعه زنی حتماً باید یک مرحله جلوتر از مرحله مونتاژ اولیه باشد و هرگونه تأخیر در این مرحله باعث بیکار شدن مونتاژکاران میشود، گاهی خرابی گیوتین که در کارگاهها بهوفور پیش میآید، موجب عقب ماندن در این مرحله میشود. پس باید طوری مرحله قطعه زنی پیش برود که با خرابی دستگاه برای مدت طولانی نیز قطعه برش خورده برای عملیات مونتاژ وجود داشته باشد.
3.2.5. تمیزکاری و سندبلاست اولیه
کلیات مواد خام، قبل از ورود به سالن قطعه زنی، تمیزکاری (زنگزدایی) میگردند زیرا ممکن است ورقهای خریداری شده سطحی روغنی و زنگ آلود داشته باشند. عملیات سند بلاست، اسیدشویی و استفاده از برسهای سیمی در این مرحله به سبب بالابردن کیفیت جوش قطعات صورت میگیرد.
4.2.5. برش کاری و پخ زنی
برش ورق توسط گیوتین هیدرولیکی و دستگاه Co2 برش، هوابرش، پلاسما و … صورت میگیرد. همچنین برشکاری پروفیلهایی مانند میلگرد، نبشی، تیرآهن توسط دستگاههای برشکاری مقاطع، از جمله ارهلنگ و اره آتشی انجام میگیرد. پس از انجام برشهای اصلی، به دستگاه برش حرارتی زاویه داده میشود و این بار با انجام برش زاویهدار، پخ لازم به لبهها جهت انجام جوش شیاری داده میشود.
شکل 29 – پخزنی
5.2.5. تسمه سازی؛ یکسره کردن ورقهای و انجام جوش درزهای آنها روی شاسی و بازرسی جوش درزها
تسمه سازی فقط در مورد اعضای ساخته شده از ورق به کار میرود. ازآنجاییکه ورق بهصورت رول برش نخورده و یا اغلب به طول ۶ متری برش خورده در بازار موجود میباشد و از طرفی اکثر دستگاههای برش گیوتین، قابلیت برش ورق تا طول حداکثر ۶ متر را دارا میباشند، جهت ساخت اعضای سازه ای نظیر ستونها و یا حتی شاهتیرها که دارای طول بیش از ۶ متر میباشند، تسمه سازی امری اجتنابناپذیر میباشد. در تسمه سازی باید از تسمه ورقهایی صاف و بدون پیچیدگی و یا شمشیری شده استفاده شود. مونتاژ و یا سرهم کردن صحیح تسمهها و رعایت محل قرارگیری بندهای جوش در قطعه نهایی از نکات بسیار مهم در کیفیت نهایی و کارایی تیرورق ها میباشد.
در مرحله مونتاژ، تسمهها روی یک شاسی مسطح در راستای یک سری صفحات عمودی کوچک (بهصورت لچکی) که از قبل باید بهصورت ریسمانی در یک راستا قرار گرفته باشند، قرار میگیرند و درزجوشها همراستا شده و با خالجوش به هم متصل میشوند. قطعاتی که با جوش شیاری بهصورت لببهلب به یکدیگر متصل میشوند، باید هم باد یکدیگر قرار گرفته و بهوسیله پیچ، گیره، گوه، قید و یا خالجوش تا اتمام جوشکاری در وضعیت خود تثبیت شوند. در صورت امکان استفاده از قید و قالب، توصیه میشود، آزادیهای مناسب برای جمعشدگی و تابیدگی وجود داشته باشد.
شکل 30 – برش تسمهها با دستگاه راسته بر
شکل 34 – شاسیکشی و مونتاژ ستون
– برای جوشکاری پلها با دستگاه زیر پودری، جوش باید بهصورت ضربدری اجرا شود و ساق جوش باید در نقشهها دیده شود تا طبق آن آمپر و ولتاژ تنظیم گردد.
– برای جلوگیری از افتادگی بال پلها باید از گیره زدن ورق به بال پل از رو و یا نصب مهاری پشت سرجوش در فواصل مختلف استفاده کرد.
– این نکته را بهخاطر داشته باشید که پس از انجام جوش زیر پودری به علت رطوبت و ناخالصی پودر، حفراتی در جوش به وجود میآید که حتماً باید بهصورت دستی پر شود.
– شاسیکشی و جوشکاری باید توسط افراد ماهر انجام شود تا از دوبارهکاری، صرف هزینه و وقت اضافه پرهیز شود.
شکل 35 – مونتاژ ستون
شکل 36 – مونتاژ تیر
8.2.5. مونتاژ و جوشکاری تکمیلی
در این مرحله، قطعات الحاقی از جمله کف ستون و پلیتهای تقویتی، قطعات زیرسری و کله گاوی، مونتاژ سختکنندههای داخل ستون و سایر الحاقات هسته ستون و یا مونتاژ وجه چهارم در ستونهای جعبهای، معمولاً بهصورت دستی توسط پرسنل مجرب و آموزشدیده به سازه اصلی اضافه میگردند و جوشکاری تکمیل میگردد. در این مرحله، مونتاژکار با تعیین فاصله قرارگیری ملحقات بر اساس نقشه، اقدام بهقراردادن اجزای فرعی در محل صحیح خود و ثابت کردن آن توسط خالجوش مینماید.
شکل 37 – مونتاژ تکمیلی ستون
شکل 38- مرحله مونتاژ تکمیلی نصب سخت کننده داخل ستون قوطی
شکل 39- مرحله مونتاژ و جوشکاری تکمیلی
شکل 40- مرحله مونتاژ و جوشکاری تکمیلی – آمادهسازی بدنه برای اتصال بعد چهارم ستون
9.2.5. ساخت قطعات فرعی
همزمان با ساخت قطعات اصلی و به طور موازی، ساخت قطعات فرعی (ورق بادبند، دستک طرهها و …) صورت میگیرد. مصالح خام این قطعات نیز مانند قطعات اصلی، تمیزکاری، برشکاری، سوراخکاری و مونتاژ نهایی میگردند.
شکل 41- اعضای قطری بادبند تکمیل شده
برای درک بیشتر از مطالب این بخش به ویدئوهای زیر مراجعه کنید.
در ویدئو زیر میتوانید یک فیلم کوتاه از سازه اجرا شده و نکات مربوط به آن را تماشا کنید.
در این بخش باتوجهبه نامبردن دستگاههای برشزنی توضیحات مختصری درمورد انواع دستگاههایی که در مرحله فوقالذکر استفاده میشود ارائه میگردد.
10.2.5. انواع دستگاه برشکاری در کارخانه
دستگاه برش گیوتین هیدرولیک:
این نوع از دستگاه، دومین نسل از برشهای هیدرولیکی است که میتواند یک ورق را با حرکت یکنواخت خطی و با یک تیغه نسبت به تیغه دیگر برش دهد. زاویه برش را میتوان در یک محدوده مشخص تنظیم کنیم که این قابلیت میتواند تغییرشکل برشی ورق فلزی را کاهش دهد و در صنایع مختلف میتواند، ورقهای فلزی بسیار ضخیم را برش دهد.
شکل 42- دستگاه برش گیوتین هیدرولیک
دستگاه راسته بر:
این دستگاه جهت تولید تسمه (برشهای خطی) استفاده میشود که جایگزین بسیار مناسبی برای تجهیزات گرانقیمتی مانند گیوتین میباشد. این دستگاه با داشتن چندین هد هواگاز (تعداد قابل تغییر) و قابل تغییر به هد پلاسما به طور همزمان میتواند چندین تسمه را تولید نماید.
با دستگاه راسته بر مشکلات معمول تولید تسمه از قبیل پیچیدگی و در اصطلاح شمشیری شدن و داشتن پلیسه برطرف گردیده و از نظر کیفی برشهایی مطابق با آئیننامههای مربوطه را تولید نمود.
دستگاه پخ زن میتواند پخهای X,Y را به طور همزمان در طول تسمهها ایجاد نموده و با این روش، فرایند آمادهسازی تسمهها برای مراحل بعدی کار به حداقل میرسد. با استفاده از امکان عرضی بر میتوان در هر طولی تسمهها را برش داده و تنظیم طول تسمهها را با دقت بالا انجام داد.
شکل 43- دستگاه راسته بر
دستگاه CNC برش پلاسما:
از این دستگاه میتوان برای برش و سوراخکاری قطعاتی با ضخامت از ضخامت 0/2 میلیمتر تا 20 میلیمتر با دقت ±0/01 میلی متر استفاده نمود.
شکل 44 – دستگاه برش پلاسما
دستگاه لیزر برش CO2:
این دستگاه برای برش دقیق فلز و غیرفلز استفاده میشود. از این دستگاه در صنعت استفاده زیادی میشود؛ چراکه عملیات برش را با دقت و سرعت بالایی انجام میدهد. با کمک آن میتوان بر روی اجسام مختلف برش و سوراخکاری کرد و یا اشکال مختلف را بر روی مواد حک نمود. در این نوع از دستگاههای لیزر میتوان فولاد را تا ضخامت ۱٫۵ میلیمتر برش داد
لیزر برش CO2 برای برش و حکاکی در صنایع کاربرد دارد. دارای 2 عملکرد میباشد:
- برش حرفهای یا Cut
• سوراخکاری یا Hole
شکل 45- دستگاه لیزر برش
دستگاه هوابرش:
هوابرش نوعی دستگاه برشکاری است که برخلاف انواع دیگر با گازها انجام میگردد. در این سیستم، دستگاه برقی وجود ندارد و با استفاده از دو کپسول که حاوی گازهای متفاوت میباشند، فعالیت مینماید. از سیستم هوابرش در برشکاریهای آهن بهوفور استفاده شده است.
شکل 46- دستگاه هوابرش
دستگاه برش پلاسما:
دستگاه برش پلاسما، پلاسما براثر خروج گاز نجیب توسط یک نازل روی سطح مادهای که قرار است برش داده شود، ایجاد میشود. با استفاده از دستگاه برش پلاسما که یکی از روشهای مدرن و پیشرفته و البته پیچیده برش فلزات است، برش فلزات بسیار راحت شده است. با استفاده از دستگاه برش پلاسما میتوان با دقت و سرعت بالا اقدام به برش مواد مختلف رسانا از جمله فلزات کرد.
شکل 47- دستگاه برش پلاسما
دستگاه دریل رادیال:
ماشینهای دریل بهمنظور سوراخکاری نقطهبهنقطه بر روی قطعاتی همچون در بخش قالبسازی که در کارگاههای کوچک بهمنظور سوراخکاری قطعات کوچک قالب استفاده میشود.
شکل 48 – دستگاه دریل رادیال
شکل 52- ماسه سیلیکا
گارنت:
یکی دیگر از سایندههای متداول در تمیزکاری پاششی، گارنت است. این ماده هزینه بیشتری نسبت به ماسه سیلیسی دارد اما در صورت استفاده صحیح، کیفیتی برابر با آن خواهد داشت. بهعلاوه، گردوخاک حاصل از بهکارگیری گارنت در سندبلاست کمتر است و تنفس آن خطری را برای سلامت کارکنان ایجاد نمیکند.
شکل 53 – گارنت
استارولیت:
استارولیت، مخلوطی از ماسههای ریزودرشت است که سیلیس بسیار پایینی دارد. این ساینده برای برداشتن پوسته و خوردگیهای سطوح فولادی بدون ایجاد گردوخاک زیاد مورداستفاده قرار میگیرد.
شکل 54- استارولیت
آلومینا و کاربید:
مواد سنتزی نظیر کاربید سیلیسیوم و آلومینا (اکسید آلومینیوم)، بهعنوان جایگزینهای رایج ماسه شناخته میشوند. این سایندهها از دوام بیشتری برخوردارند و گردوخاک کمتری تولید میکنند. مواد سنتزی معمولاً قابل بازیابی و استفاده مجدد هستند. آلومینا تقریباً برای آمادهسازی هر سطحی (شیشه، گرانیت، مرمر و فولاد) مناسب است.
شکل 55 – آلومینا
مشخصات ساینده بر روی عملکرد سندبلاست تأثیر مستقیم دارند. از ویژگیهای مهم سایندهها میتوان به موارد زیر اشاره کرد:
- ابعاد: هر چه ابعاد ساینده بیشتر باشد، سطح زبرتر خواهد بود.
2. چگالی: چگالی پایینتر باعث نرمی بیشتر سطح میشود.
3. قابلیت بازیابی: امکان جمعآوری و استفاده مجدد از ساینده، هزینه فرایند سندبلاست را کاهش میدهد.
4. سختی: سختی بالاتر، طول عمر و قابلیت استفاده مجدد از ساینده را بهبود میبخشد. درصورتیکه چگالی و سختی بالا باشند، عمق نفوذ نیز افزایش مییابد.
5. شکل: ذرات کروی شکل باعث ایجاد سطح صاف/شفاف و ذرات تیز باعث ایجاد سطح زبر/کدر میشوند.
4.3.5. دستگاه و تجهیزات متداول سندبلاست در سازههای فولادی
بر اساس نوع کاربری و حجم تمیزکاری، سیستم تجهیزات ساب پاشی به سه نوع سندبلاست قابلحمل، کابین سند بلاست و اتاق سندبلاست تقسیم میشوند. باتوجهبه موضوع قابلبحث در ادامه به معرفی ویژگیها و کاربردهای سیستم سند بلاست قابلحمل خواهیم پرداخت.
دستگاه سند بلاست قابلحمل:
یکی از تجهیزات پرکاربرد برای اجرای تمیزکاری پاششی سطوح کوچک تا بزرگ، دستگاه سندبلاست قابلحمل یا پرتابل است. اجزای سندبلاست پرتابل عبارت هستند از:
- کمپرسور هوا: تولید هوای فشرده
2. دیزل ژنراتور: تأمین انرژی موردنیاز برای راهاندازی کمپرسور هوا
3. دیگ: مخزن تحتفشار برای نگهداری ساینده و هدایت آن به سمت شیلنگ
4. شیلنگ: واسط بین دیگ و نازل برای خروج ساینده و اعمال آن به سطح
5. نازل: محل خروج ساینده با فشار بالا
سیستم سندبلاست قابلحمل، معمولاً توسط یک کمپرسور دیزلی تغذیه میشود. کمپرسور هوا، حجم بالایی از هوای فشرده را به دیگ سندبلاست وارد میکند. در دیگ سندبلاست، میزان ساینده خروجی قابل تنظیم است. در این سیستم میتوان از چندین دیگ تحتفشار نیز استفاده کرد. سیستمهای مجهز سندبلاست پرتابل معمولاً بر روی کامیون نصب میشوند. این کار، قابلیت جابهجایی راحت تجهیزات را بهبود میبخشد.
شکل 56 – دستگاه سندبلاست قابلحمل
شکل 57 –سازه فولادی در حال سندبلاست
شکل 58 – سند بلاست
شکل 59 – وت بلاست
شکل 60- سند بلاست(شکل بالا)، وت بلاست (شکل پایین)
شکل 61 – شات بلاست
شکل 62 – گریت بلاست
برای اطلاعات بیشتر در مورد روش اجرا سند بلاست به ویدئو زیر مراجعه نمایید.
4.5. انتقال و نصب سازه فلزی پیچ و مهره ای و جوشی در پروژه
-هنگام مونتاژ اسکلت فلزی و نصب ستونها و تیرها تا زمانی که جوشکاری لازم انجام نشود و یا حداقل نصف پیچومهرهها بسته نشده باشد، کابل نگهدارنده جرثقیل از قطعات در حال نصب جدا نمیشود.
اطلاعات بیشتر : Steel frame factory
-قبل از نصب قطعه ساخته شده بر روی تیر یا ستون، قطعه زیرین صددرصد پیچومهره یا جوشکاری میشود.
– تیرها و ستونها بلافاصله پس از نصب و جوشکاری و یا پیچومهره شدن از نظر اطمینان به انجام صحیح و کامل کار مورد بازدید قرار میگیرند. هنگام بالابردن قطعات فلزی ساخته شده توسط جرثقیل، جهت جلوگیری از نوسان شدید قطعات و ایجاد حادثه، بهوسیله چند رشته طناب و به طور دستی حرکت آنها کنترل میگردد.
-در هنگام بارندگی یا وزش باد شدید یا مواردی که به علت ناکافی بودن روشنایی، احتمال حادثه افزایش مییابد باز ادامه عملیات برپایی اسکلت فلزی جلوگیری به عمل میآید.
-کلیه اجزای اسکلت فلزی عاری از هرگونه مواد زاید و لغزنده میشوند.
-هنگام برپایی اسکلت فلزی از ورود افراد به داخل منطقه خطر جلوگیری میگیرد.
فلوچارت مراحل ساخت اسکلت فلزی در کارخانه را در زیر مشاهده می کنید:
شکل 65- فلوچارت مراحل ساخت اسکلت فلزی
نتیجه گیری
۱- ساخت اسکلت فلزی توسط کارخانه به علت وجود تجهیزات کاملتر، نیروی متخصص، وجود یک برنامه زمانبندی برای تولید و همچنین وجود واحد نظارتی و کنترل کیفیت، پیروی از ضوابط و آییننامهها و انجام تستهای مربوطه، از درجه کیفی مطلوبتر و ایمنی بالاتری برخوردار است.
۲- ساخت اسکلت فلزی دارای مراحل متعددی است که بسیاری از این مراحل مربوط به پیش از تولید میباشد که نقش اساسی و به سزایی در تولید یک اسکلت باکیفیت و اقتصادی دارد.
۳- برای تهیه نقشههای شاپ، شاپیست باید بهدقت نقشهها و ضوابط را چک کند و تغییرات لازم را با هماهنگی دستگاه مشاور اعمال نماید تا سازه بهصورت بهینه و اصولی تولید شود.
4- نقشههای شاپ دارای بخشهایی متفاوتی است و برای تولید قطعهها، مونتاژ و نصب و برپایی سازه تهیه میشود.
5 -از طریق نقشههای شاپ لیست مصالح و کارت برش تولید میشود.
6- برای ساخت اسکلت فلزی در ابتدا قطعههایی که در آینده قرار است به هم متصل شود و اجزای سازهای را تولید کند را با دستگاههای مخصوص از ورقهای فولادی برش میدهند. هم زمان با برش قطعات سوراخکاری و پخزنی انجام میگیرد.
7 – در مراحل بعدی، مونتاژ، جوشکاری و تستهای نهایی و در صورت نیاز ترمیم، سند بلاست، ضدزنگ و رنگکاری انجام میشود.
8-پس اتمام تولید با تأیید دستگاه نظارت سازه بستهبندی، بارگیری و به محل اجرا حمل میشود.
منابع
مسیر یادگیری برای حرفه ای شدن
- فرایند ساخت اسکلت فلزی در کارخانه از مرحله شاپ تا اجرا همراه با 6 ویدئو جامع
- مطلبی میخواهید که نیست ؟ از ما بپرسید تا برایتان محتوا رایگان تولید کنیم!